管道树脂固化修复可应用于混凝土、钢筋混凝土等多种下水道的局部修复,能修复管道裂缝、机械磨损、腐蚀、破裂等缺陷。施工时需先对管道进行清洗和检测,确定修复位置和面积,再准备树脂材料和热固化设备,涂抹树脂后热固化,检测修复效果。其优势在于无需破坏管道、高效快速、耐久性强,能有效延长管道使用寿命,是管道修复的优选方案。
管道树脂固化修复在实际操作过程中可能遇到一些问题,了解这些问题及其相应的解决方法可以帮助确保修复工作的顺利进行,并达到预期效果。
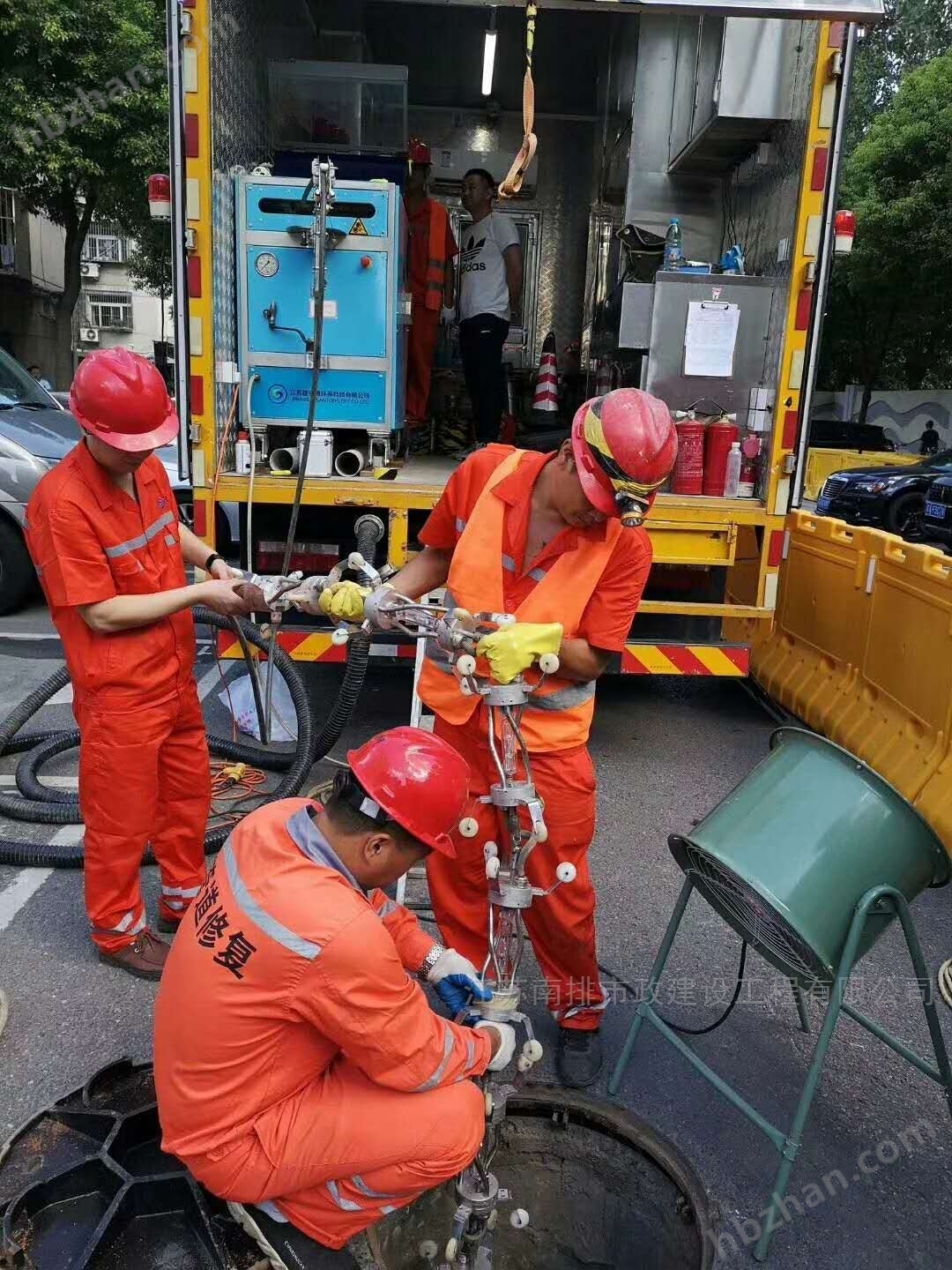
1、软管安装不贴合
问题描述:
在软管安装过程中,可能出现软管未能贴合管道内壁的情况,导致部分区域存在空隙或褶皱,这可能会影响修复效果。
解决方法:
预检查与清理:在安装前检查并清理管道内部,移除可能导致软管无法平滑展开的障碍物。
精确控制牵引力:使用适当的设备和技术手段来精确控制软管进入管道的速度和力度,确保其能够均匀展开并与管道内壁紧密贴合。
充气辅助:对于某些情况,可以通过向软管内部充气的方式帮助软管更好地贴合管道形状。
2、树脂固化不良
问题描述:
如果树脂没有按照预期充分固化,可能会导致新形成的内衬层强度不足,无法提供足够的保护作用。
解决方法:
严格遵循工艺参数:确保根据制造商提供的指南准确设置固化条件(如温度、湿度、光照强度等)。
监控固化过程:利用传感器或其他监测工具实时跟踪固化进度,及时调整工艺参数以优化固化效果。
选择合适的固化方法:根据具体情况选择适合的固化方式(热水固化或紫外线光固化),并确保所使用的设备处于良好状态。
3、树脂渗漏
问题描述:
在浸渍过程中,若树脂从软管中泄漏出来,不仅会造成材料浪费,还可能污染周围环境。
解决方法:
加强密封措施:采用高质量的密封材料和技术,在软管两端以及接缝处做好密封处理,防止树脂泄露。
适当调整树脂配方:根据不同类型的管道和工作环境,适当调整树脂的粘度和其他性能指标,提高其流动性和粘附性。
4、内衬层厚度不均
问题描述:
由于操作不当或其他原因,新形成的内衬层可能存在厚度分布不均的问题,影响整体结构的稳定性和使用寿命。
解决方法:
均匀施加压力:通过调节注入的压力或者使用专门设计的装置来保证树脂在整个软管内的均匀分布。
多次检测确认:在施工过程中多次使用CCTV等工具检查内衬层的形成情况,及时发现并纠正不均匀现象。
5、施工后出现裂缝或破损
问题描述:
尽管完成了修复工作,但有时仍会在短期内发现内衬层出现了裂缝或破损点。
解决方法:
增强质量检验:增加施工后的验收环节,仔细检查每一个细节,确保没有潜在缺陷。
及时修补维护:一旦发现问题立即采取补救措施,避免小问题演变成大故障。
管道树脂固化修复通过识别上述常见问题并采取有效的预防和应对策略,可以大大提高成功率,延长管道的使用寿命,同时减少不必要的返工和成本支出。